Manipulator With Air Shaft
driven by air actuators have been developed as a multifunctional final actuator for material handling systems. The arm consists of a pneumatic hand and a gas wrist. The industry robot can grip a variety of objects without force sensors or feedback control. In factory automation applications, air manipulators are charged with compressed air to speed up the process of work. Some factories are dependent on automated pneumatic systems to direct product ingredients into the appropriate conveyor of stainless steel on the line, and the factory can keep the equipment running 24 hours a day as the factories increase productivity.
The working principle of air manipulators
Air manipulators operate using gas compression, which is based on the principle of the hydrodynamic principle working under the concepts of stress. In addition, any mechanism using pneumatics uses a set of interconnected components: the gas circuit is made up of the combination of the gas compressor, the bridge tube, the gas container, the hydraulic hoses, the open gas and the actuated components. An aerodynamic industrial manipulator starts with the the compressor that generated the compressed air. It then moves to a reservoir where the air is stored. Then buttons control the gas flow and a circuit controls the motion of the valves to move the gas between the components that require it. Finally, the manipulator's actuator uses the air to do the work. The gas operated industrial manipulator consists of a base and several actuators. This number varies according to the design of the industrial manipulator. Its base or shoulder is part of the arm and sits on the floor or on a raised surface, providing a stable base for the rest of the industrial manipulator. Actuators: The upper arm, elbow, forearm, wrist and above hand components make up the pneumatic industrial manipulator that allows it to work. Each part can be controlled individually for more accurate control.
Pneumatic systems in the hands of air manipulators
Pneumatic systems form an original and unique category of pneumatic industrial machinery control engineering. They are classified as "fluid power control", which describes any process or device that converts, transmits, distributes or controls power through the use of pressurised gases or liquids. In a pneumatic system, the working fluid is a gas (mainly air) that is compressed above atmospheric pressure to transfer pressure energy to molecules. The stored pressure potential is converted into suitable mechanical work in a suitably controlled sequence using control valves and actuators. Pneumatic systems are ideally suited to the automation of simple repetitive tasks. The nature of the working fluid is abundant and therefore the operating and maintenance costs of these systems are very low. Pneumatic systems allow a variety of power conversions for smaller mechanical hardware. Conversion of various motion combinations such as linear to rotary and rotary to linear is possible. The simple design, durability and compact dimensions of the pneumatic systems make them ideal for mobile applications. These features make them versatile and find versatile applications including industrial robotics, aerospace technology, production and assembly of automotive components (power steering, chassis and engine assembly), CNC machine tools, the food and packaging industry, bomb deployment units and manufacturing processes for plastic products.
The article focuses on knowledge related to air manipulators and one of the benefits of browsing through the article is that they can move very smoothly. Pneumatic industrial manipulators operate using gas compression, which is based on the principle of fluid mechanics working under the concept of pressure. In addition, any pneumatic device used uses a set of interconnected components: the pneumatic circuit is made up of a gas compressor, a transition tube, a gas tank, a hose, open air and passive components.
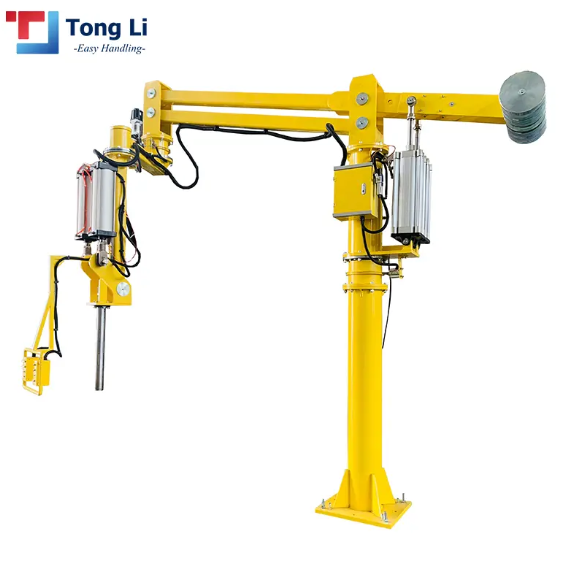
Post time: Nov-10-2022