The use of pneumatic manipulator is becoming more and more widespread, but do you know what its components are? Do you know what are their roles? Below Tongli will explore this industrial robot with you.
Structure of the parts of pneumatic manipulator
The industrial robot consists of a base, a column, cylinder components, a brake, a storage tank, a number of rotating joints, an operating handle and a fixture, etc. It is one of the most common pieces of manipulator robots nowadays. The manipulator is able to move and turn at will within its range of activity, and we generally refer to the movable joints as degrees of freedom.
1. The base: Ensures that the industrial robot does not shift when transporting heavy objects, and that it can transport large and small objects in a very stable manner. Basically, it will not hang or fall, it is very solid.
2. Column: The equipment generally uses a rigid column, which has good support. Even if the weight of the object is heavy, it will not be shaken when handling.
3. Cylinder: It mainly plays the role of balancing the load of the jig, which can make heavy objects easy to carry and save labour.
4. Components: The pneumatic manipulator will often carry large items and will rely mainly on components to ensure the quality of the product when carrying.
5. Brakes: To ensure that the parts do not operate when the manipulator robots stop working.
6. Air storage tank: Used as a backup air source.
The components of pneumatic manipulator
- Components: Industrial manipulator involve pneumatic components such as oscillating cylinders, duplex cylinders, pen-type cylinders and air source processing components.
- The air source handling unit: Consists of a pressure regulating filter, an air inlet switch and an elbow. The air source is provided by an air compressor, with a pressure range of 0.6 to 1.0 MPa, and an output pressure of 0 to 0.8 MPa, which can be adjusted. The output compressed air is sent to each working unit.
- Pen cylinder: The material is sent to the corresponding position by the reciprocating movement of the cylinder. If the direction of the incoming and outgoing air changes, the direction of movement of the cylinder will also change. The magnetic switches on both sides of the cylinder are mainly used to track whether the cylinder has moved to the specified position.
- Double coil solenoid valve: Mainly to control the cylinder into and out of the air, to achieve the expansion and contraction movement of the cylinder. Be aware of the red indication of the positive and negative lights, if the positive and negative terminals are reversed, it can also work, but the indication is in the closed state.
- Single coil solenoid valve: Control the cylinder of the single direction movement, to achieve the expansion and contraction movement. The difference with the double coil solenoid valve is that the initial position of the double coil solenoid valve is not fixed and can control two positions at will, while the initial position of the single coil solenoid valve is fixed and can only control one of the directions.
Main sensors of pneumatic manipulator
The industrial robot detects its own state, such as speed, position and acceleration, through the internal sensors of the perceptron, which in turn interact with environmental information, such as distance, temperature and pressure, which is detected by external sensors. In the next step, the corresponding environmental mode is selected by the controller to direct the robot to complete the task. The sensors used inside the manipulator robots are mainly the following.
1. Photoelectric sensors
Principle: The detection light from the emitter is irradiated to the object to be measured and then diffuse emission occurs, after the receiver receives a strong enough reflected light, the photoelectric switch starts to act.
- Inductive proximity switch
Principle: The inductive proximity switch has an oscillator inside which generates an alternating magnetic field. When the induction distance reaches a certain range, eddy currents will be generated within the metal target, thus making the oscillation strength weaken. The oscillator oscillation and the change of stopping vibration are processed by the amplifier circuit behind and finally converted into a switching signal.
- Cylinder piston in place detection ---- magnetic switch
Principle: After the cylinder piston with magnetic ring moves to the specified position, the two metal pieces inside the magnetic switch close under the action of magnetic field and trigger the signal.
The working principle of the pneumatic manipulator
The industrial robot is mainly composed of the control system execution, drive system, actuator and position detection system. Under the control of the PLC program, the actuator moves through the pneumatic drive.
The information of the control system transmits the command to the actuator, tracks the manipulator robots action and will immediately alarm if an error or fault occurs in the action.
The actual position of the actuator is transmitted to the control system using the position detection device, which ultimately moves the actuator to the specified position with a certain degree of accuracy.
Extra knowledge
The compressed air used in the pneumatic drive of the industrial robot contains mainly moisture, which, when utilized directly, might impair the cylinder's performance and corrode the workpiece. To remove the moisture from the compressed air, a water separation device must be installed. Select compressed air that is less than 6 kg/cm2, use a pressure reduction valve to regulate the gas pressure, and make sure that the accumulator has adequate gas on hand. To make sure the pressure doesn't drop while the gas is used by the fuel tank. The pneumatic robot's speed will slow down and its motion will be out of tune because of the low gas pressure. Therefore, a pressure relay is required on the air circuit, when the air pressure is lower than the specified pressure, the circuit is broken and the work stops which can protect the pneumatic manipulator well.
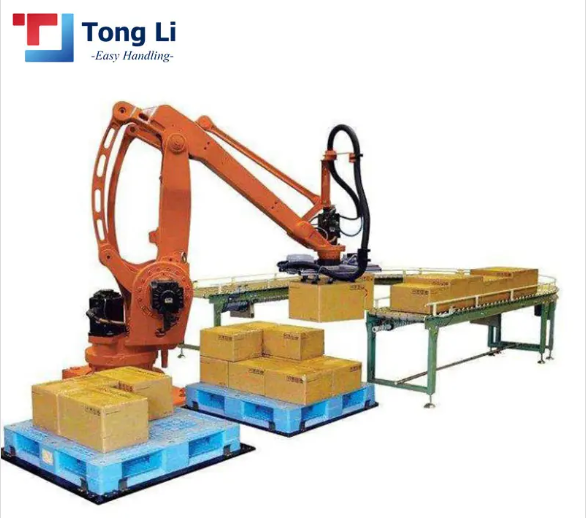
Post time: Nov-16-2022