With the widespread use of pneumatic manipulators, do you know the basic principles of their work? Tongli will tell you in detail.
A pneumatic manipulator consists of a base and several actuators. This number varies according to the design of the industrial robot. Its base or shoulder is part of the arm and sits on the floor or a raised surface, providing a stable base for the rest of the handling robots. Actuators: The upper arm, elbow, forearm, wrist, and above-hand components make up the air manipulator that allows it to work. Each part can be controlled individually for more accurate control.
The pneumatic manipulator consists of an actuator, a drive system, a control system, and a position detection device. Under the control of the PLC program, the pneumatic drive system is used to realize the corresponding parts of the actuator, in a sequence, with movement trajectory, with a certain speed and time. At the same time, the information of the control system is used to issue commands to the actuators.
The compressed air used in the pneumatic transmission of the robot often contains moisture, which can affect the work of the cylinder and corrode the workpiece when used directly. Therefore, a water separation device needs to be set up to separate out the moisture in the compressed air. Generally, choose less than 6kg/c㎡ of compressed air, need use the pressure-reducing valve to control the gas pressure, and accumulator reserve enough gas to ensure that the cylinder consumption of gas, pressure does not decrease.
As the gas pressure is low, the robot speed is slowed down, and the action is out of tune, so the gas road need to place a pressure relay, when the air pressure is lower than the prescribed pressure, the circuit is broken, and stop working.
Air manipulators operate using gas compression, which is based on the principle of fluid mechanics and works under the concept of pressure. In addition, any pneumatic device uses a set of interconnected components: the pneumatic circuit is made up of a gas compressor, a transition tube, a gas tank, a hose, open air and, passive components.
Pneumatic manipulators start with the compressor that generates the compressed air. It then moves to the reservoir where the air is stored. Valves then control the airflow and a circuit controls the valves to move the air between the components that require it. Finally, the actuators of the handling robot use the air to carry out the work.
The movements of the air manipulator can be monitored if necessary, and an alarm signal is given when there is an error in the movement or a fault occurs. The position detection device feeds back the actual position of the actuator to the control system at any time and compares it with the set position, which is then adjusted by the control system so that the actuator reaches the set position with a certain degree of accuracy.
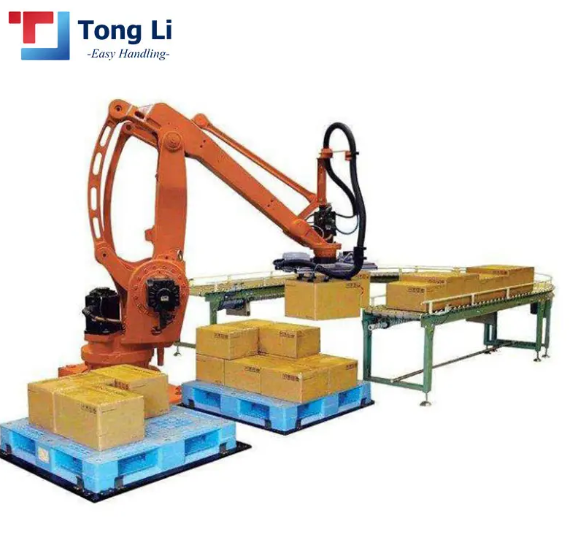
Post time: Dec-08-2022